One of the worst nightmares for a production manager is when a key piece of machinery fails and you’ve forced stop production and lose critical time and money. Something as dreaded as this only needs to happen once to keep you up at night worrying until the root cause has been found and preventative measures have been put in place to ensure it doesn’t happen again. Wilfley recently had the opportunity to ease the troubles of a customer in need and hopefully help them sleep a little easier at night.
The Problem
A large copper mine in Mexico was using an automatic pressure filter to extract and dry molybdenum at the final stage of their process. Unfortunately, the customer has had issues in the past when the diaphragm in the filter deformed to such an extent that they would need to shut down the filter for repair. The filter in this application would have processed just over 2.6 US tons of moly in the typical amount of time it took to replace the diaphragms, which translated to roughly $36,000 worth of lost production time. Additionally, parts and labor for the repair averaged around $15,000.
After some troubleshooting, it was determined that the failure was caused by an excessive amount of water entering the pressure filter, which deformed the diaphragms due to an improper balance of water and solids. The excessive water that was causing this imbalance was coming from the seal flush system that was needed for the competitor pump that fed the filter.
The competitor pump used traditional compression packing, which required as much as 6 gallons (23 liters) of flush water per minute to maintain proper sealing. This might not seem like much but it quickly adds up to 5,180 gallons (19,610 liters) of additional water entering the filter per day, assuming roughly 60% enters the process. The customer needed a solution and the clock was ticking until the next failure occurred.
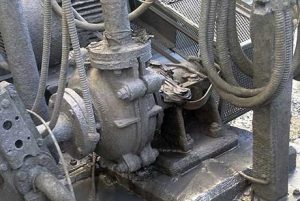
The Solution
The solution couldn’t have been simpler… replace the competitor pump with an EMW® slurry pump in MAXALLOY® 5A with SolidLock® sealing technology. The SolidLock® static seal combined with the dynamic expeller seal provides leak free operation at all times without requiring the type of flush systems that are needed for conventional sealing systems like compression packing and mechanical seals.
Without the need for flush water, the customer would no longer need to worry about excessive water entering the pressure filter and diaphragm failures. And with the EMW® slurry pump costing 75% less than the lost production time and associated expenses of a single failure; the solution was a home run.
The Happy Ending
The EMW® slurry pump has now been in operation for almost a half of a year and both the pump and the pressure filter have been running trouble free. The customer is extremely happy with the outcome and can finally get a good night sleep.
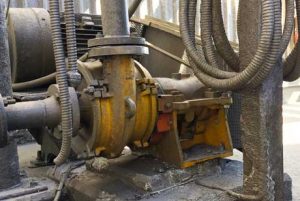