The Problem
A large ethanol producer in Kansas was fed up with the wear life of the pumps in some of their key applications. One of their more problematic pumps was in an application that fed a fine slurry made up of corn and milo grain into a flash vessel. This is a particularly difficult application because milo grain is especially abrasive (compared to corn grain) and also because the flash vessel is located early enough in the process that there is still a significant amount of sand in the slurry mix. The existing pump in this application was a competitor pump in standard CD4 (ASTM A890) with a mechanical seal. The plant performs a scheduled shutdown every six months to inspect and repair equipment and they were routinely finding that the wet end parts (case, impeller, and backing plate) had worn out beyond repair and that the mechanical seal was leaking profusely. During a typical shutdown, the pump would require replacement of the impeller, case, backing plate, and mechanical seal at a minimum. The costs were definitely adding up.
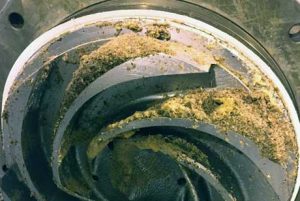
The Solution
The Wilfley sales team proposed to replace the existing competitor pump with an A9 heavy duty chemical pump in WCD4™ duplex stainless steel with SolidLock® sealing technology. The A9 pump would be the same ANSI size as the competitor pump so minimal work would be needed to exchange them.
Wilfley’s WCD4™ is a specially processed duplex stainless steel that is chemically similar to standard CD4 (ASTM A890) but with significantly improved mechanical properties. WCD4™ has a typical hardness of 345 HBN, which is 1.5 times harder than the CD4 used in the competitor pump. The superiority of WCD4™, as well as the heavy-duty construction of the A9, would have a serious impact on the wear life of the pump.
The SolidLock® static seal has proven to be the preferred alternative to conventional sealing technologies like mechanical seals and compression packing, especially in applications containing abrasive solids. The simple but very effective design and non-contacting seal faces during operation maximizes the life of the seal and ensures trouble-free operation.
(Sample data based on pin-on-disk testing)

The Happy Ending
The A9 pump was installed last October (2016) and just recently reached its first 6 month shutdown and inspection. The case, impeller, and case plate all showed minimal signs of wear and the SolidLock® showed no signs of leakage. The pump was cleaned up, reassembled, and has been put back in service for the next six months. The maintenance team even determined that there was so little wear on the case and impeller that there was no need to adjust the impeller clearances before putting it back into operation.
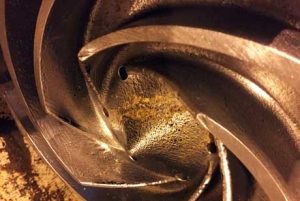
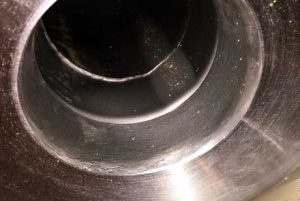